Its a process used by engineers and product designers to ensure that a product is designed to be easily and cost-effectively manufactured. This helps you build a product that makes sense for your business. It’s impossible to make money if your product is too expensive to manufacture and that’s where design for manufacture is vital.
This process involves a combination of industrial design, engineering, manufacture, injection moulding, and the use of various plastics.
Its an iterative design process that involves the use of various industrial design principles and techniques, as well as an understanding of how both injection moulding and different types of plastics can be used. This process can start as far back in the conceptual stage when your product is being developing by the industrial designer, all the way through to when you are working with the manufacturer.
Design for manufacture also helps to reduce the amount of waste generated during the manufacturing process. By designing products with fewer components and fewer steps in the manufacturing process, designers and engineers can reduce the amount of time and resources needed to produce the product. In other words, the DFM process helps you reduce your costs.
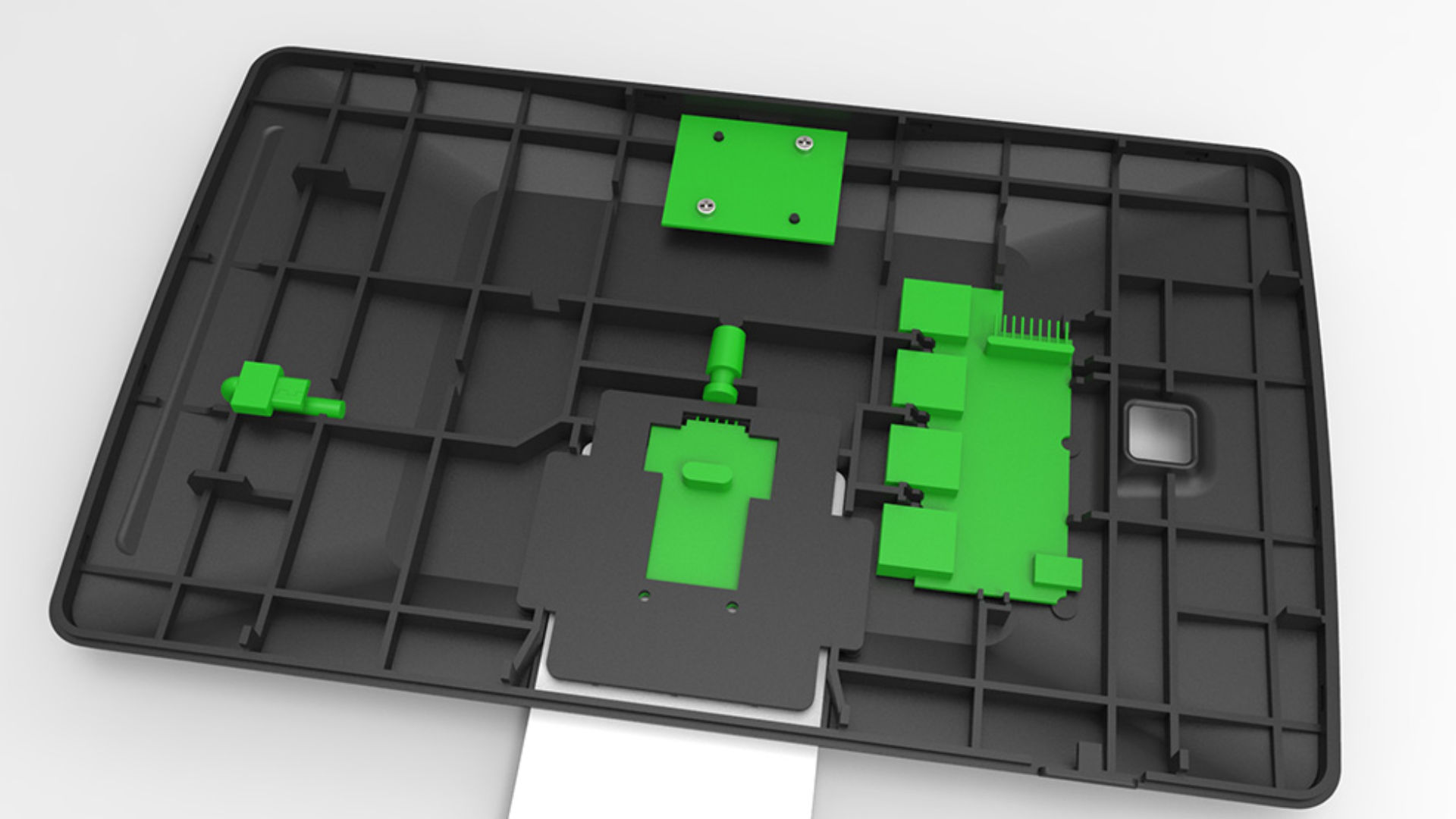
One of the main goals of DFM, is to reduce the cost of materials used in the manufacturing process, as well as the cost of labour associated with the production of the product. All of these considerations help you build a product that works for your business. This point can be one of the most crucial steps in helping your product become a success, never skip an opportunity to eliminate a part or process as long as it doesn’t affect your products overall goals.
Using design for manufacture to design a product has several advantages.
- It can reduce the cost of production by ensuring that components are easy to manufacture with minimal wastage.
- Reduce the lead time for production by ensuring that designs are optimised for efficient manufacturing.
- Result in high-quality products due to its focus on precision and attention to detail.
- Facilitate the use of various materials and components while ensuring that they are used in the most cost-effective manner.
- Help to improve the safety of a product by ensuring that components are designed to meet safety standards.
- It can also help to reduce the environmental impact of a product by ensuring that components are designed to be as energy-efficient as possible.
- Help to improve the overall user experience by ensuring that components are designed to be as user-friendly as possible.
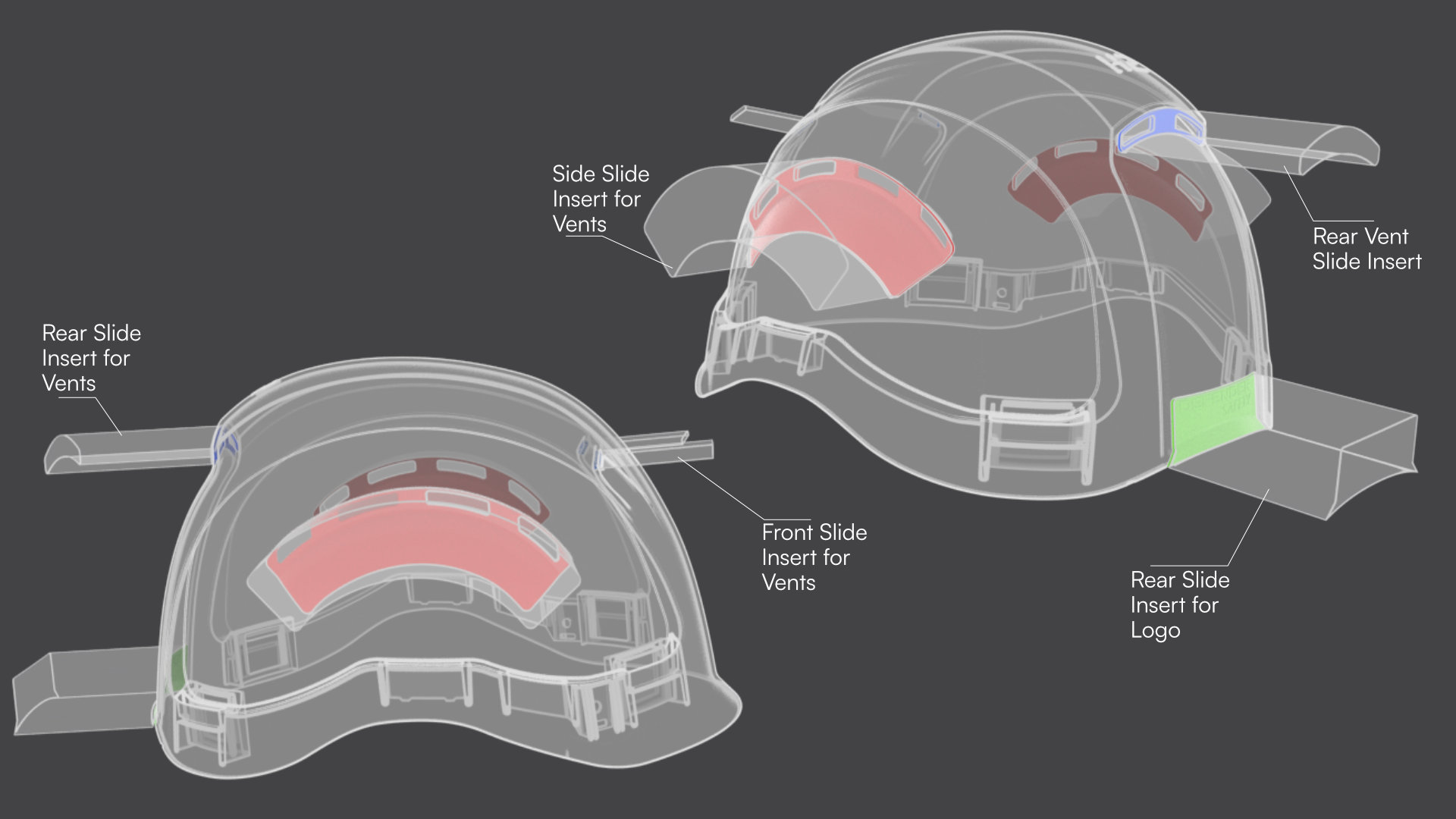
What does Industrial Design have to do with design for manufacture?
Industrial designers are important when developing a product for mass production. When you hire an industrial designer with your idea, it’snot just the look and feel that you should be looking for, its how they goabout creating a business smart product.
There are a few the basic principles we as industrial designers apply to every product designed:
- Ergonomics and usability refer to designing a product with the user in mind, making it logical, thoughtful and easy to use.
- Aesthetics are important as they determine how attractive a product appears and how the product fits in with the brand.
- Strength, and structure is necessary to ensure that the product can withstand wear and tear.
- Environmental conservation refers to designing a product with sustainability in mind.
- Usability. This means that the product should be easy to use and understand, and should be intuitive for the user.
- Cost-effective design is essential for manufacturers as it allows them to keep production costs low.
- Last but not least, manufacturability and assembly
The last two pints might be the most valuable part to your projects success. If your design cannot be manufactured or manufactured for the right price, you don’t have a business. So, while in the beginning stages of iterating an idea it’s okay to not be too strict with if it can be manufactured or not. As you get to a stronger concept, manufacturability is incredibly important to think about and you should learn to prioritise designing for manufacture as much as possible.
What happens if you don’t prioritise designing for manufacturing? It’s normally right at the end, when you approach an injection mould company. You have a beautiful render or prototype. But moulding has not been thought about.
We have seen designs change as much as 60% from the original design just to make it manufacturable. Whereas if manufacturing and moulding were thought about from as early in the process as possible. When the design goes through the design for manufacture stage, it might only change 5%/10% in looks/function.
Hiring an industrial designer or product engineer that understands manufacturing and injection moulding will help save you heaps of time and tears when you get to the manufacturing part of your project. It may seem expensive now. But when you’re dropping $50 000 on a mould, you want that design to be as efficient as possible.
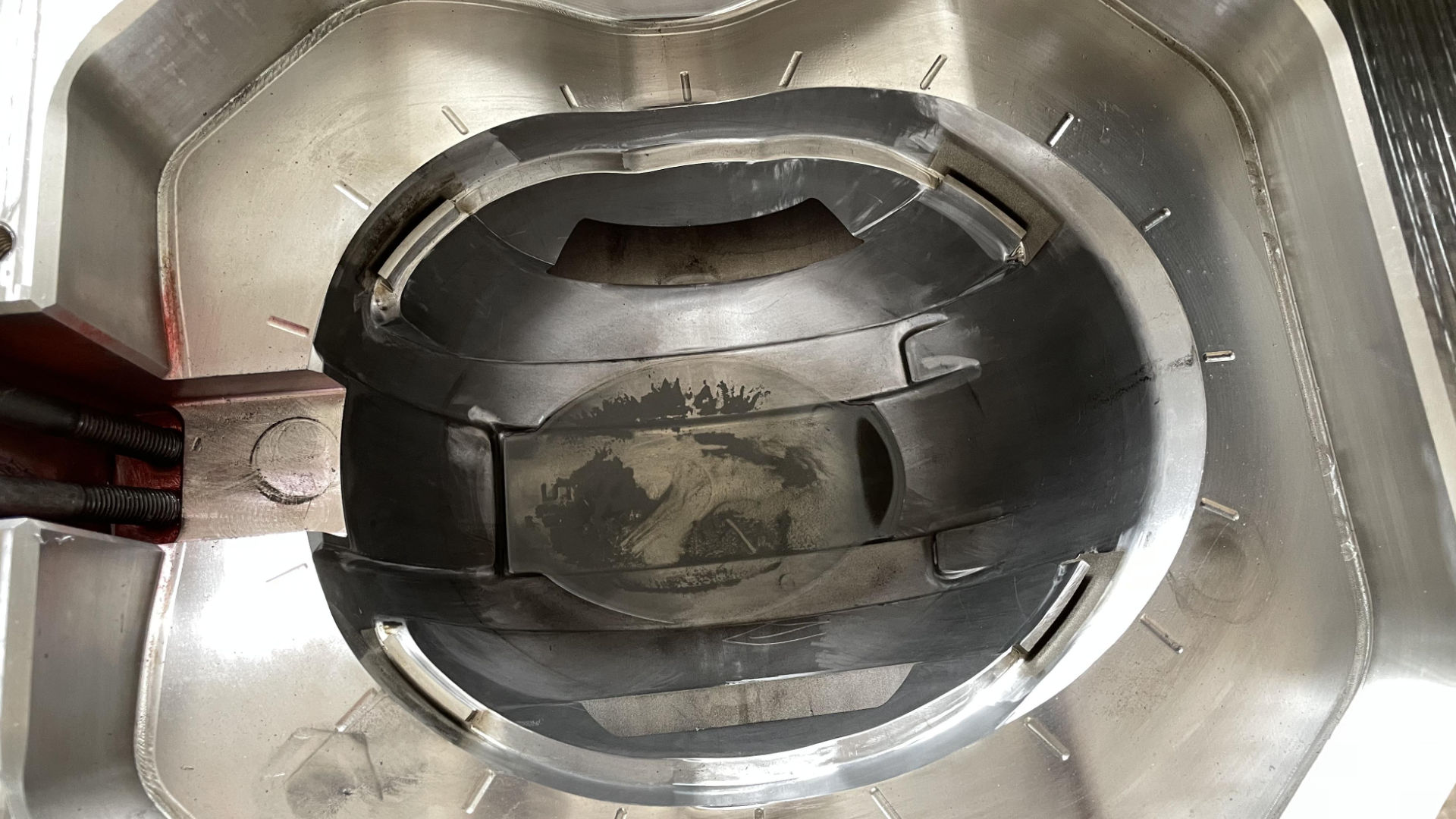
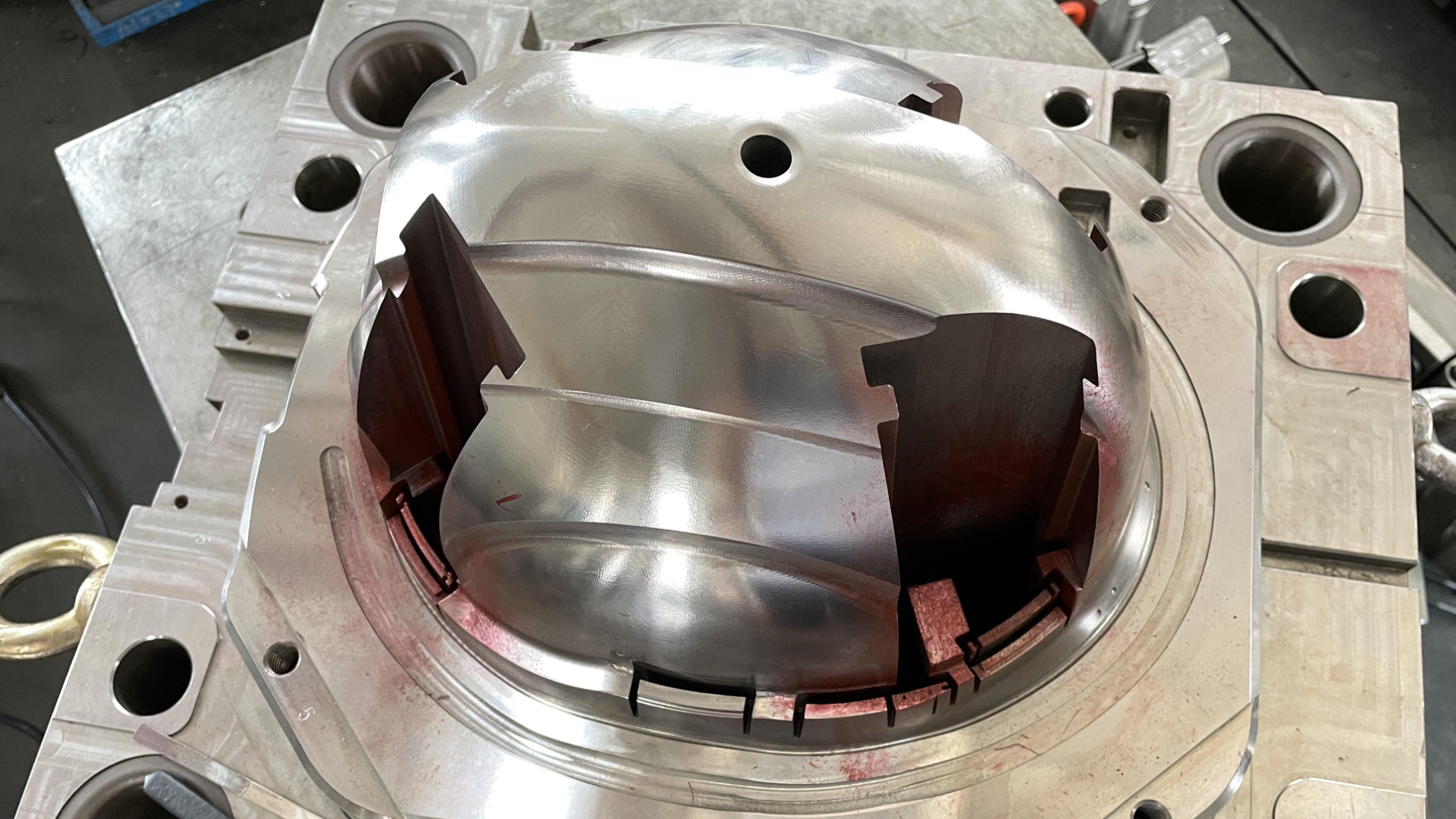
So now that we know how important designing for manufacture is. Let’s talk a bit about injection moulding:
Injection moulding is a manufacturing process used to produce parts or components with intricate shapes and designs. It consists of a heated cylinder into which molten plastic is injected at high pressure. The plastic is then forced into a mould cavity where it cools and solidifies in to the desired shape. This process can be used to produce components with highly accurate shapes and sizes, making it ideal for use in design for manufacture.
Injection moulding is a cost-effective way to produce large quantities of parts quickly and efficiently. The moulds normally carry a large initial cost with the option to produce up to 1 million parts with that mould. The actual parts have a low cost and once you can pay off the moulds, injection moulding is very cost effective. Because of the moulds large cost, it is vital that you plan on selling a couple thousand products and more. Not a hundred.
Injection moulding also allows for the use of a wide range of materials which can range from soft flexible plastics to hard, fibre reinforced plastics.
Advantages and Disadvantages of Injection Moulding
While Injection moulding has been the king for several decades. It definitely has its pros and cons.
Pros:
- It is fast, efficient, and cost-effective, meaning that parts can be produced quickly and at lower costs than other processes.
- It is capable of producing components with highly accurate shapes and sizes, making it ideal for use in design for manufacture.
- The surface finish can be immaculate
Cons:
- It requires expensive machinery and moulds, as well as skilled labour for operation.
- It is not suitable for producing components with complex designs.
- And as you now know, it requires the designers and engineers to have a good understanding of the process to build parts that are injection mould friendly. So it comes with a large setup cost (design time and moulds)
Overall, just like anything in life. Injection moulding has its use. If your engineer or designer understands the variety of manufacture methods like injection moulding, high volume 3D printing and vacuum casting for example. You can choose the right method for your business, and your product. That’s the beauty of understanding what technologies are out there. You can optimise your design for the manufacturing technology, as well as plan for different manufacturing as your product sales increase.
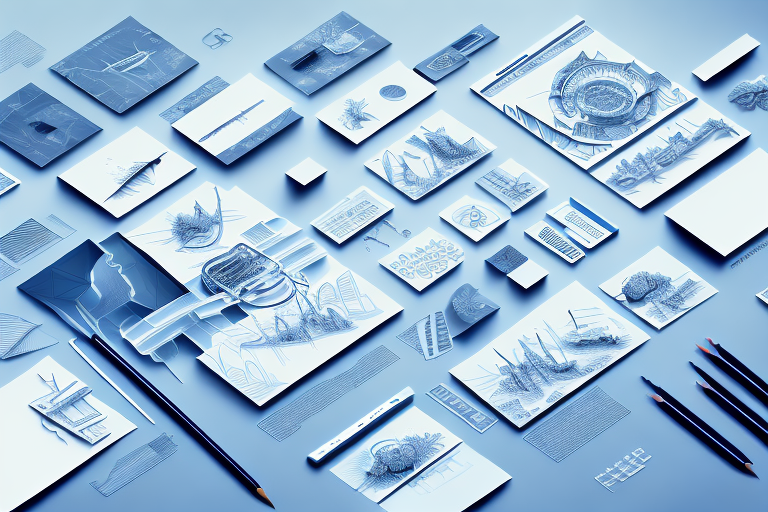
Design for manufacture and design for injection moulding, is an important process used us industrial designers to create products that can be easily and cost-effectively manufactured. It involves a combination of design principles, manufacturing techniques, money and strategy to produce a solution that makes sense for your business.
And that is the key to designing for manufacture. If you are going to be producing a product in the thousands and more. It is imperative you prioritise design for manufacture so you end up with a solution that makes you money so you can sustain and grow your business.
Other Articles
More from the blog
Discover everything you need to know about taking your product to market.
Ready to turn your dream into reality?
Get customized product development assistance